To manage configurable products in an optimal way in engineering and production, you must connect Product Data Management (PDM) with product model development and a configurator.
These needs can be solved with one solution: VariSuite – an offering management system.
Let engineer manage product rules effectively during design
The fastest way to develop configurable products is to give engineers a system that allows them to create, manage, and test product models in parallel with the new design. A technical product model often creates order-based items and product structures for production. VariSuite is a system for managing product model complexity with items and product structures, which can include design documents and change or revision control.
Use the product model also in sales
The technical product model is used as basis for the sales model; you can use the rules from the product model and add pricing rules to the sales model. This way both sales and production have a consistent picture of the product in the whole organization.
PDM with product model and configurator increases data quality
Like most PDM solutions, VariSuite has all the standard capabilities: item and product structure management with a product configurator, document management, change and classification management, search and reporting. With VariSuite, engineers can create and test a product model with parameters and configuration rules already in the design phase. This will shorten the product lead-time and improve quality as it is no longer necessary to make a separate configurator after design work.
If I have PDM already, but not configurator?
If company already has a PDM system for standard items, VariSuite provides product models and an integrated configurator that can be used with the existing system. (This is called bi-modal usage.) VariSuite also offers standard PDM functionality for engineering areas that are not supported by your current PDM.
Support your production with configurator
Once the engineers have created product models, the product configurator generates order-based product configurations with order parameters and creates new items with order-based identifiers and structures for production. The related design data and manufacturing documentation can be connected to new items. If necessary, the production configurator can be run automatically as part of order processing.
Order-based items and structures can be saved as product individuals in the VariSuite database to gather information for service or maintenance. Data for product individuals is shown in a simplified way from service perspective.
Integrate VariSuite seamlessly
VariSuite can be integrated to any system with an API, for example, to ERP with standard item and BOMs as well as order-based items and BOMs. VariSuite has integrations to MS Office, allowing users to create documents directly from MS Office tools, and to most CAD systems to integrate CAD models, items, structures, and drawings in different formats. Product model can be integrated to some CAD systems to generate new geometry and order-based drawings and file formats for production.
Common parameters and product modularity
Product models can refer to a set of configuration parameters, which are recorded in the VariSuite database with identifiers, descriptions, and allowed values. The parameter set should be managed with a process that guides product designers to use existing parameters instead of adding new parameters for each new product.
A configurable component is modeled in VariSuite as an independent component with its own configuration parameters. The component can then be used in many products and subassemblies as long as the higher-level component provides values for all parameters of the configurable component. If you have complex product rules or multilevel product structure, VariSuite can help you.
Easy to use and to share product data for whole organization and partners
VariSuite has a web interface, which is mainly used for reading and for rather straightforward data modification, and a desktop client, which is mainly used for more complex data modification, including product model manipulation. Both user interfaces can use predefined queries and structure views, which can be created by ordinary users for their personal use and by system administrators for all users or selected user groups. The flexible access rights allow you to share product data with partners and subcontractors and show them only the data they need.
Extend VariSuite for the present and future needs of your organization
The data model can be modified easily. For example, a new item type and attributes for this type can be created by a user with necessary access rights. The new item type appears automatically in user interfaces when the user must select types for a new or existing item. Similarly, the attributes of the new item type appear automatically when a user interface shows attributes of an instance of this type.
Additional functionality is implemented with a script mechanism without any changes in the generic application server, which is identical in all VariSuite installations.
Case KONE: Faster time-to-market and order-to-delivery process
Variantum shortens KONE’s time-to-market by providing adaptable product modeling tools. Variantum digitizes the order-to-delivery process and integrates it with aftersales. KONE has used Variantum technology for managing configurable products since 2009.
You can read more about the case here: case KONE
KONE is a global leader in the elevator and escalator industry. KONE provides elevators, escalators and automatic building doors, as well as solutions for maintenance and modernization to add value to buildings throughout their life cycle.
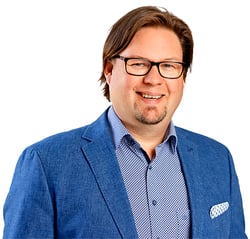
Teemu Kaattari
Head of Products